Effective noise control is essential in modern building environments, particularly where comfort and productivity are priorities. Sound attenuators—also known as duct silencers—are critical components in HVAC systems, designed to minimize noise transmission through ductwork and maintain acoustic comfort in occupied spaces. (1)(3)

Fundamental Concepts
What is Sound?
Sound is a propagating vibrational disturbance or wave in an elastic medium (solid, liquid or gas). Sound is most commonly thought of as being transmitted in air and detected by a person’s ears.
What is Noise?
Noise is defined as any unwanted or undesirable sound. While sound in general is not necessarily a problem and may even be desired in certain situations, when it is unwanted or annoying, we refer to it as noise. The proper application of Noise Control Products such as silencers and panels are discussed in this engineering guide.
Frequency
Frequency describes how many cycles an oscillation completes in one second. Humans can typically hear sounds ranging from 20 Hz to 20,000 Hz. To simplify the process of measuring and analyzing this wide spectrum, the frequency range is divided into octave bands, each defined by a specific center frequency. The standard octave bands used in HVAC noise assessments include: 63 Hz, 125 Hz, 250 Hz, 500 Hz, 1000 Hz, 2000 Hz, 4000 Hz, and 8000 Hz. For more precise analysis, these bands can be further split into 1/3 octave bands.
Sound Pressure Levels
Sound travels through the air as pressure variations above and below the normal atmospheric pressure. The amplitude of these pressure changes directly affects how loud the sound is perceived. Since the human ear can detect an exceptionally wide range of pressure fluctuations, acoustics uses the decibel (dB) scale to represent sound pressure levels. This logarithmic scale compresses the vast range into more practical, readable values.
The Science Behind Sound Attenuators
Principle of Insertion Loss
Insertion loss is the primary metric for evaluating the effectiveness of a sound attenuator. It is defined as the reduction in sound pressure level (measured in decibels, dB) achieved when the attenuator is installed between a noise source and a receiver. The concept and measurement of insertion loss are fundamental in acoustical engineering and are thoroughly detailed in educational texts and standards such as ISO 7235:2009 and ASTM E477. (1)(2)
“Insertion loss is the difference in sound pressure level of a system with and without a silencer”

Pressure Drop
Installing a sound attenuator introduces a pressure drop in the airflow path. This is the reduction in static pressure from the inlet to the outlet of the silencer, caused by the resistance to airflow. Pressure drop must be carefully considered, as excessive values can increase the energy consumption of fans and affect HVAC system performance. The design goal is to achieve the desired noise reduction while minimizing pressure drop. (1)(2)
“Pressure Drop is the consequence of creating obstruction in airstream”

Acoustic Performance
The acoustic performance of a sound attenuator depends on several factors:
- Geometry and Length – Longer attenuators generally provide greater insertion loss.
- Absorptive Material – The type, thickness, and density of the material affect sound absorption, especially at different frequencies.
- Airflow Velocity – Higher velocities can increase self-generated noise and reduce effectiveness.
- Internal Baffles – These can enhance attenuation by increasing the path length and surface area for sound absorption. (1)(2)(3)
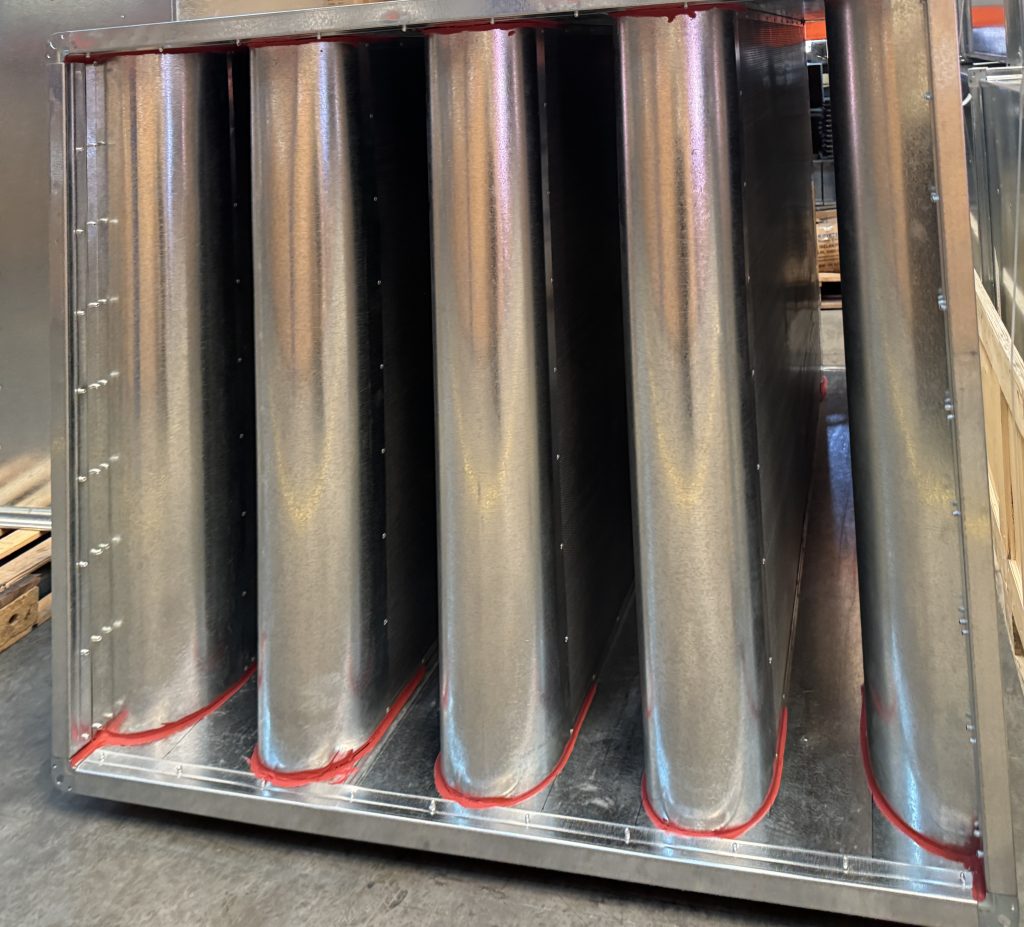
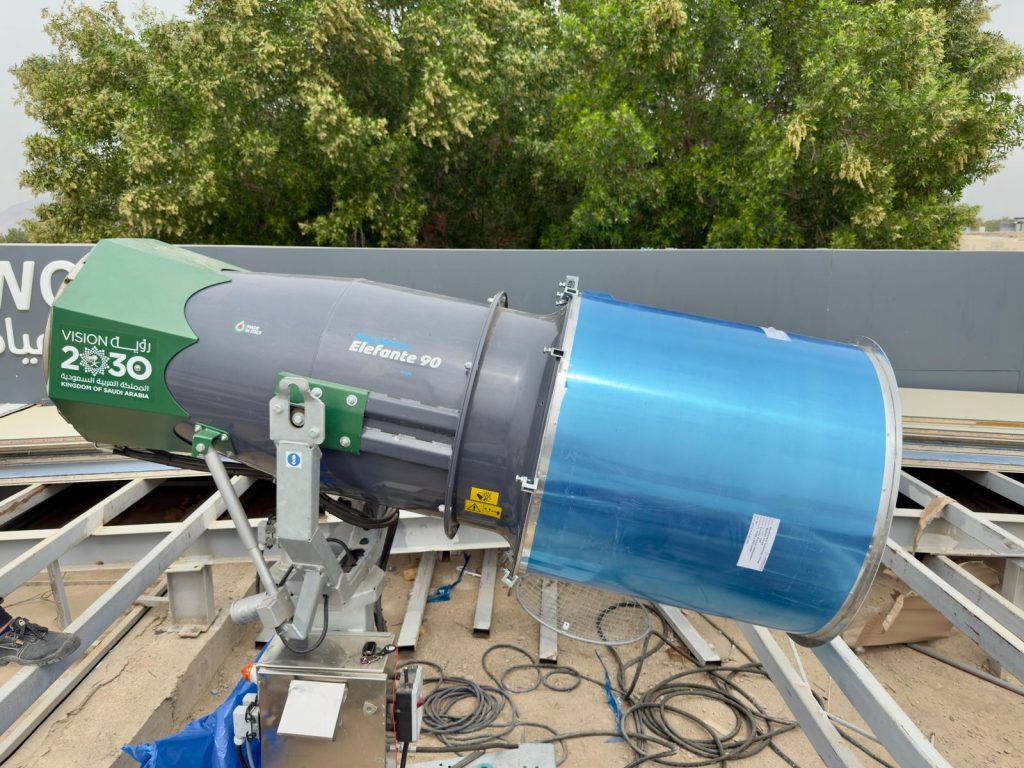
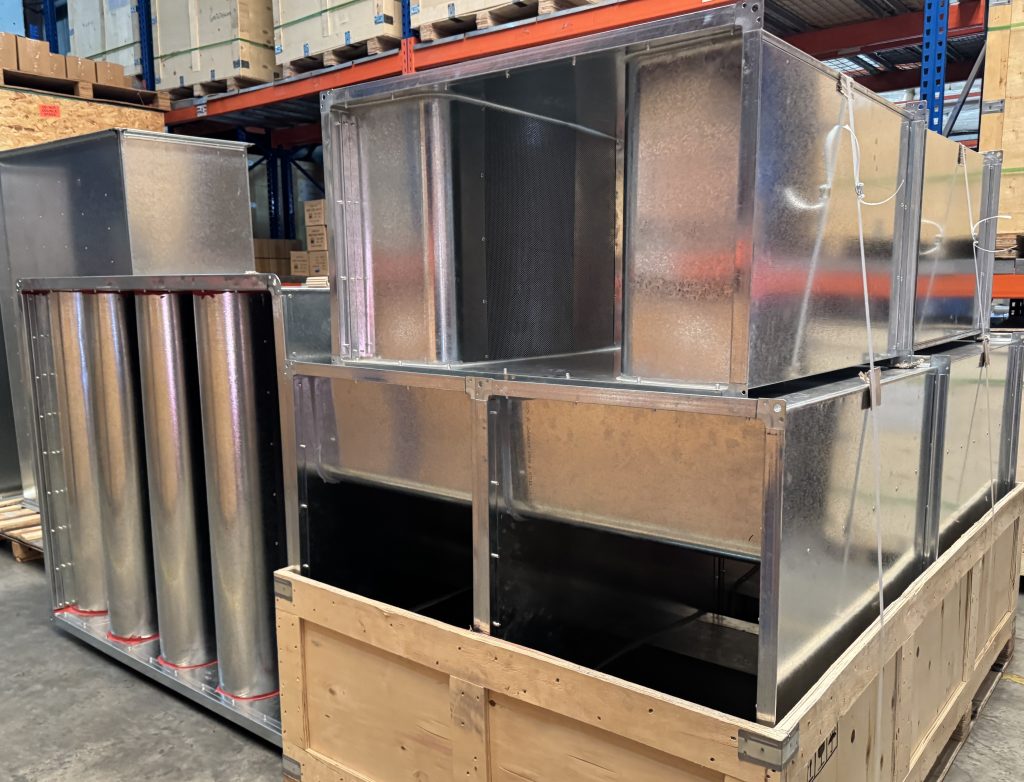
Standardized testing, as outlined in ASTM E477 and ISO 7235, ensures that attenuators meet specified acoustic and aerodynamic performance criteria. (2)
Types and Applications of Sound Attenuators
At Kinetics Group, we fabricate a wide range of sound attenuators, common types include:
- Rectangular duct silencers – are a widely used solution for reducing noise in ducted air systems. Their simple construction and cost-efficiency make them a top choice for achieving excellent sound attenuation with minimal impact on airflow. Designed for versatility, they can be easily incorporated into any HVAC setup. With various configurations available—including options for both low and high pressure drops, and different acoustic media—they are suitable for systems operating at velocities ranging 0- 2500 fpm.
- Generator room silencers – are also rectangular in shape and only differ in construction and internal baffle design, which are specifically engineered to handle high sound power levels, back pressure, and thermal loads typically generated by engine exhaust and ventilation systems.
- Circular silencers – are ideal for systems that use round ductwork, offering a seamless fit without the need for square-to-round transitions that can create additional pressure loss and airflow issues. They come in a variety of sizes, providing flexible options for different noise reduction levels and pressure drop requirements.
- Elbow-type duct silencers – offer similar acoustic performance to rectangular silencers but provide added flexibility, making them ideal for systems with limited straight duct runs. They deliver equal or superior noise reduction with only a slight increase in pressure drop and can be customized to fit a wide range of duct sizes without requiring transition pieces.
- Cross talk silencers – allow air to move between adjacent spaces while effectively blocking the transmission of unwanted sound. They are especially useful for minimizing speech privacy issues between rooms. Available in various designs, these silencers provide flexible solutions for a wide range of acoustic air transfer challenges.
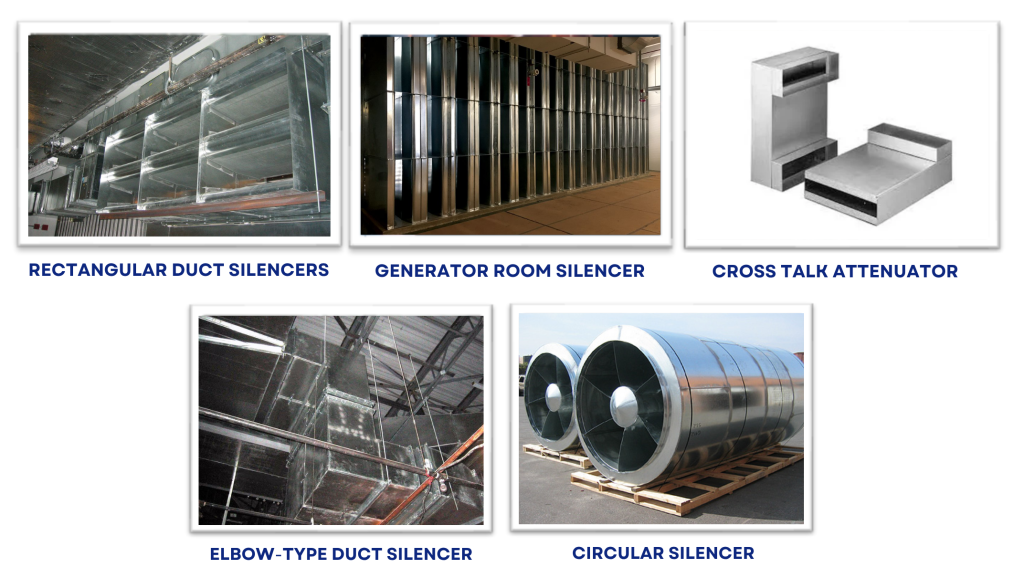
Another type of sound attenuator that KGC is capable of producing is the Packless Silencer.
Packless silencers, also known as reactive silencers, are designed without any sound-absorbing material. Instead, they are built entirely from solid and perforated sheet metal. These silencers reduce noise by incorporating multiple resonant chambers of different sizes located behind the perforated interior lining. As sound waves move through the silencer, they lose energy through a mechanism similar to that of a Helmholtz resonator, effectively lowering the noise levels at the outlet.
However, because these silencers are tuned to specific frequencies, they are less effective for reducing broadband noise. Packless silencers are generally used in environments where fiberglass or porous media are not permitted, or where the entire duct system must be sterilized—such as in cleanrooms, laboratories, hospitals, or electronics manufacturing facilities.

Common applications of sound attenuators include:
- HVAC supply and return ducts
- Industrial processes
- Recording studios
- Cinemas and auditoriums
- Hospitals and healthcare facilities
Kinetics Noise Control (KNC) Acoustics Analysis Software
The KNC Acoustic Analysis Software, developed in the USA, is an advanced acoustic simulation and calculation tool designed to support engineers and designers in:
- Attenuation Requirement Analysis – Determining the required insertion loss for specific environments based on source levels and acoustic criteria.
- System Loss Modelling – Evaluating natural sound losses through ducts, elbows, diffusers, and rooms.
- Attenuator Selection – Recommending suitable attenuator models to meet project-specific targets, in line with established engineering principles.
Below is a sample calculation that can be produced by the KNC Acoustics Analysis Software.

What Sets Kinetics Sound Attenuators Apart?
At Kinetics Group, our sound attenuators are not just built to meet industry standards—they’re designed to exceed expectations.
One of our key design advantages lies in our innovative baffle configurations, which are engineered to deliver superior insertion loss performance compared to conventional silencers. This means more effective noise reduction with minimal impact on system airflow.
Kinetics rectangular attenuator splitters are designed with a radiused leading edge and a tapered trailing edge, creating a bell-mouth type entry and exit. This aerodynamic design helps minimize self-generated noise and reduces pressure loss, enhancing acoustic performance and airflow efficiency.
We offer baffle designs made with high-performance Rockwool and Fiberglass acoustic media—materials known for their excellent sound-absorbing properties and long-term durability. These materials are strategically integrated into our attenuators to enhance acoustic efficiency without compromising airflow performance.
With a combination of advanced design and proven materials, Kinetics sound attenuators offer a unique blend of effectiveness, flexibility, and value—making them a smart choice for today’s demanding HVAC and industrial applications.
Certified Quality: Backed by Industry Standards
At Kinetics Group, we prioritize performance, reliability, and trust. That’s why our sound attenuator products are manufactured in compliance with globally recognized standards, ensuring they meet the highest technical and safety benchmarks.
We are proud to be approved in accordance with AMCA (Air Movement and Control Association International) and Intertek-certified, providing further assurance of consistent quality and reliable acoustic performance.
These certifications not only validate the integrity of our design and testing processes but also enable consultants, engineers, and project managers to specify our products with confidence.
KMCI Your Partner in Sound Attenuator Fabrication
As a proud subsidiary of Kinetics Group, Kinetics Metal Construction Industries (KMCI) in Umm Al Quwain is a regional leader in custom sound attenuator fabrication. Serving the UAE, GCC, and MENA, KMCI delivers high-quality rectangular and circular silencers, generator room silencers, elbow-type duct attenuators, and cross talk silencers for demanding applications.
Our advanced facility, commitment to international standards, and expert team ensure every product meets rigorous acoustic and performance requirements. From design to delivery, KMCI partners with clients to provide tailored solutions, technical support, and proven results.
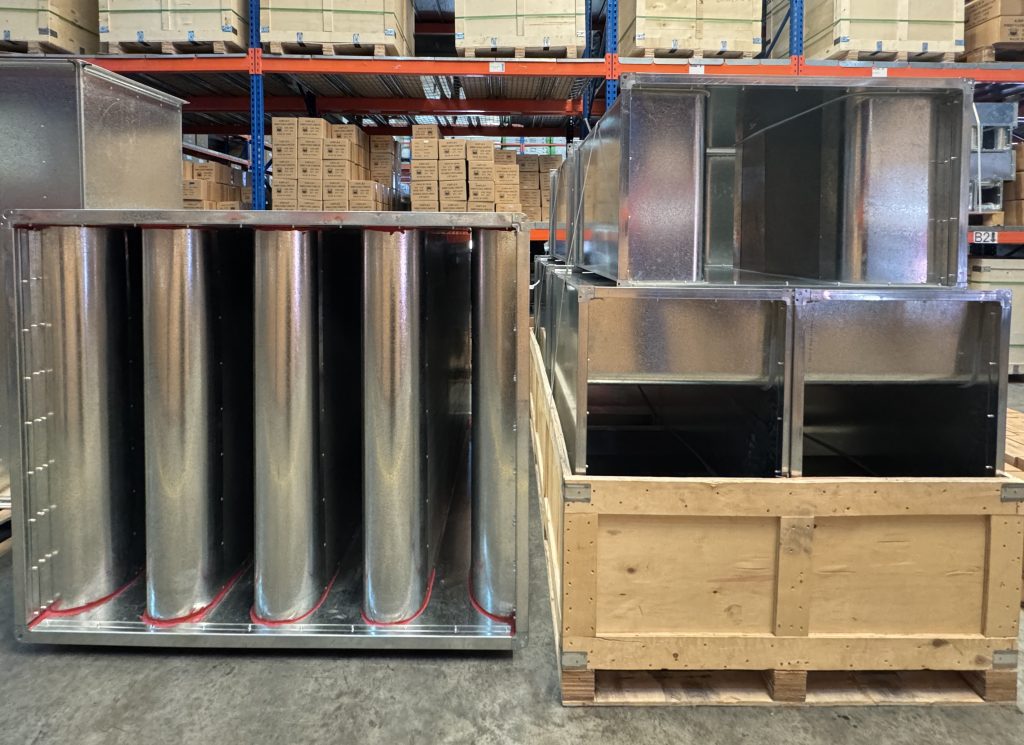
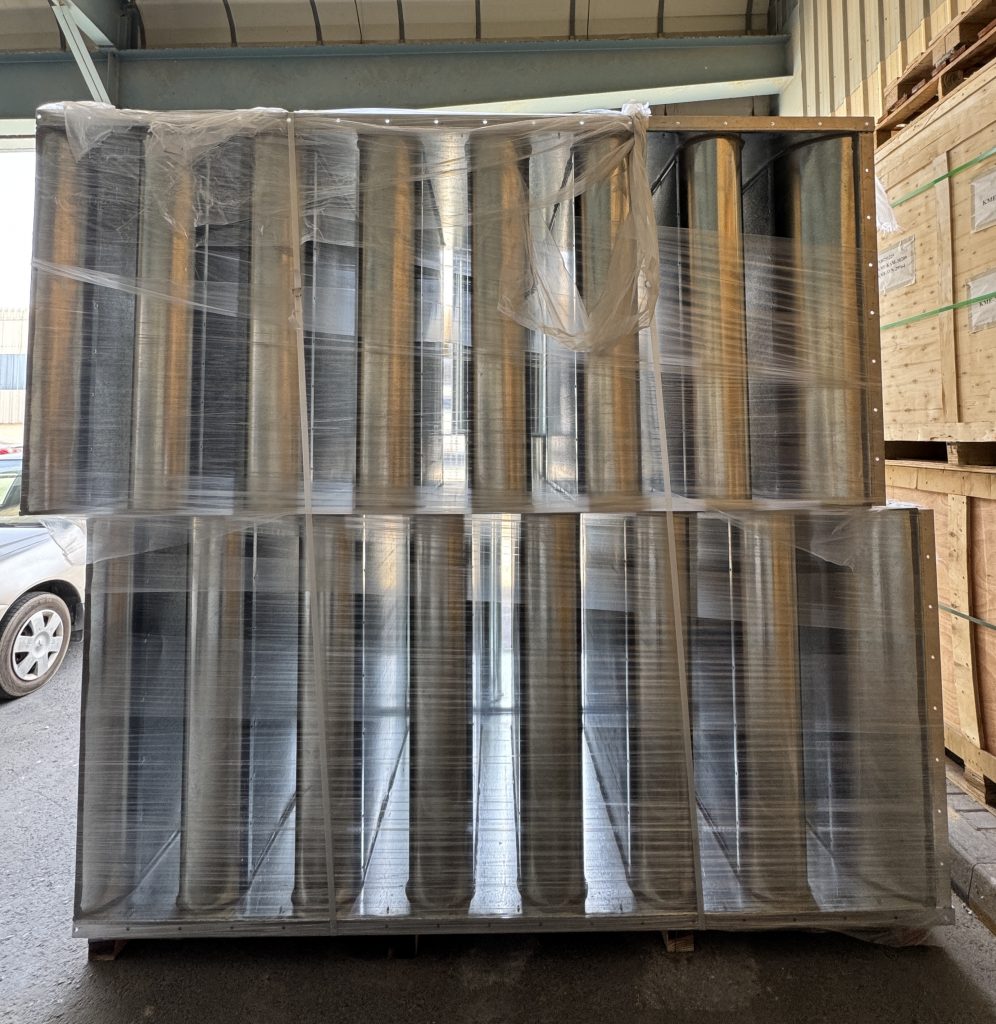
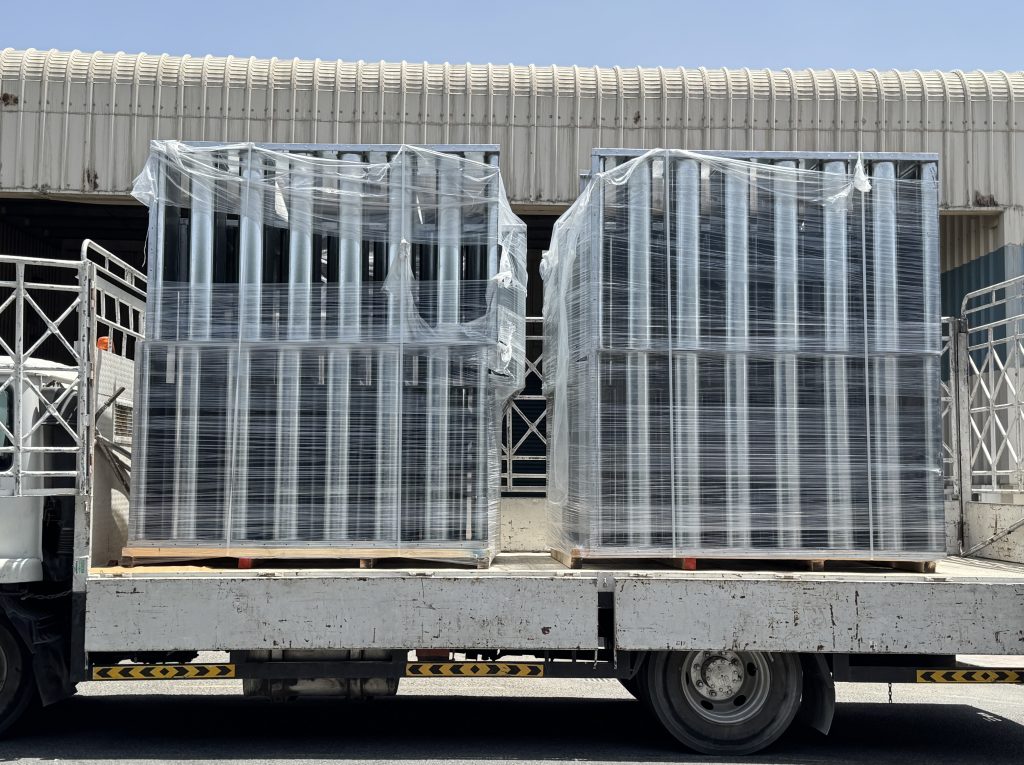
References
- Beranek, L.L., & Vér, I.L. (1992). Noise and Vibration Control Engineering: Principles and Applications. Wiley-Interscience.
- International Organization for Standardization. (2009). ISO 7235:2009 Acoustics — Laboratory measurement procedures for ducted silencers and air-terminal units — Insertion loss, flow noise and total pressure loss.
- Crocker, M.J. (Ed.). (2007). Handbook of Noise and Vibration Control. John Wiley & Sons.
- Kinetics Noise Control (Youtube): https://www.youtube.com/live/LIaqBRj00-o?si=O8_dyXXr4Ii6P81P
- https://www.amca.org/certified-listed/products.html?c=1084#kinetics-noise-control-inc
- https://kineticsgroup.ae/product-category/kinetics-noise-control-products/duct-silencers-acoustic-louvers/